智能检验:工业超声检测的进展
超声检测的演进历程
超声检测(UT)长期以来一直是工业无损检测(NDT)领域的基石,为复合材料、金属、合金及复杂几何结构部件提供关键的质量保障。随着工业领域不断引入新型材料和组件,提升超声检测方法的可靠性与实用性需求愈发迫切。在全球监管要求趋严、专业技术人员短缺以及各行业检测标准提高的多重压力下,对智能化、高效化检测方案的需求变得前所未有的紧迫。
历史上,研究与开发主要集中在优化硬件方面。然而,现代的努力则致力于将电子技术和基于软件的自动化集成到超声检测系统中。目的是尽量减少机械干预,从而提高自动化水平,改善操作员支持,并确保在减少人为错误的情况下实现更优的缺陷检测。
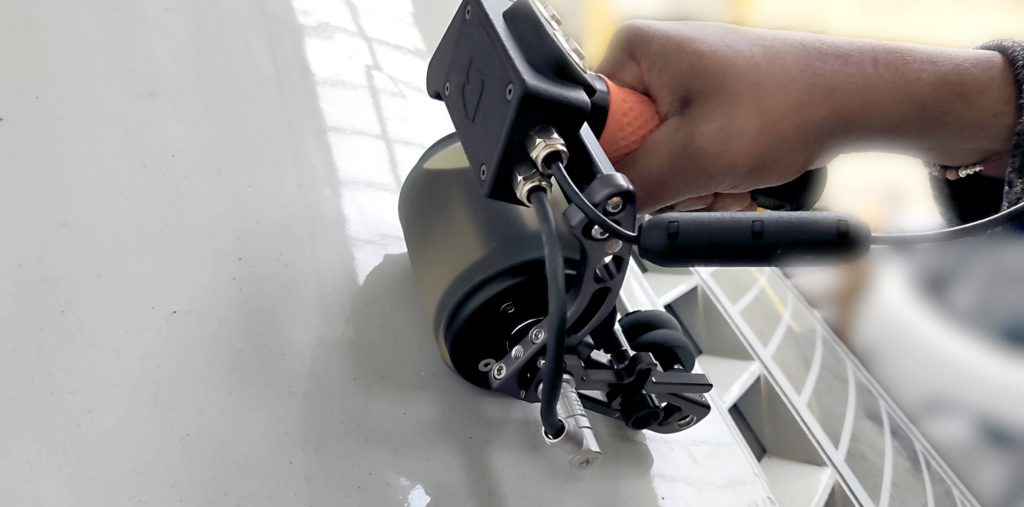
矩阵技术:超越相控阵的下一步
相控阵超声检测(PAUT)通过提供更灵活的声束控制革新了NDT。传统超声探头依赖单晶片产生一维超声波束,检测范围受限;而相控阵技术通过电子手段操控波束,实现焦点和角度的调整。然而,随着检测需求提高,行业正转向矩阵技术。矩阵超声检测采用复杂排列(如棋盘式或螺旋式)的多元素阵列收发声波,这种配置最早来源于医疗领域,能够实现多维声场的操控,提供无与伦比的灵活性、敏感性和分辨率。
相较于相控阵系统,矩阵技术的核心优势在于通过简化操作流程减少人为误差,并借助先进电子系统提升检测效率。随着时间和熟练劳动力的日益紧张,矩阵技术的自动化功能确保了更高的检验质量,同时减少了对机械干预的依赖。
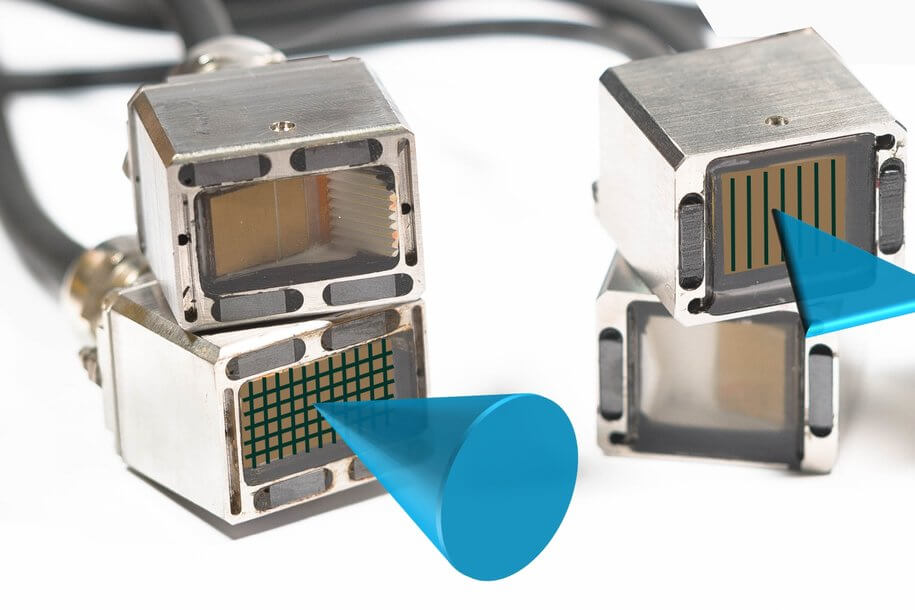
自动化在简化检测中的作用
超声检测(UT)任务中先进电子技术和自动化的整合对于实现更智能的检验至关重要。 微型化技术使得超声探头变得更小巧但更强大,特别适用于复杂几何形状零件的检验以及挑战性环境中的应用。这些创新简化了检验过程,使其变得更加便捷和高效,特别是在交通运输等行业,对于减少碳排放并满足高安全标准至关重要。
随着全球流动性的增加,对严格检测协议的需求也在增加,尤其是在铁路和航空领域。例如,中国如今拥有世界上最大的高速铁路网络,约有40,500公里的轨道。全球高速铁路网络的不断扩展凸显了有效检测系统的重要性,以确保安全性和可靠性。
同样,后疫情时代快速复苏的民航业同样需要先进NDT解决方案。随着维修、修理和操作(MRO)变得越来越重要,对智能高效检验系统的需求也在增长。专业技术人员的短缺使得对简化流程的需求更加迫切,这样才足以提升航空安全性和可靠性。
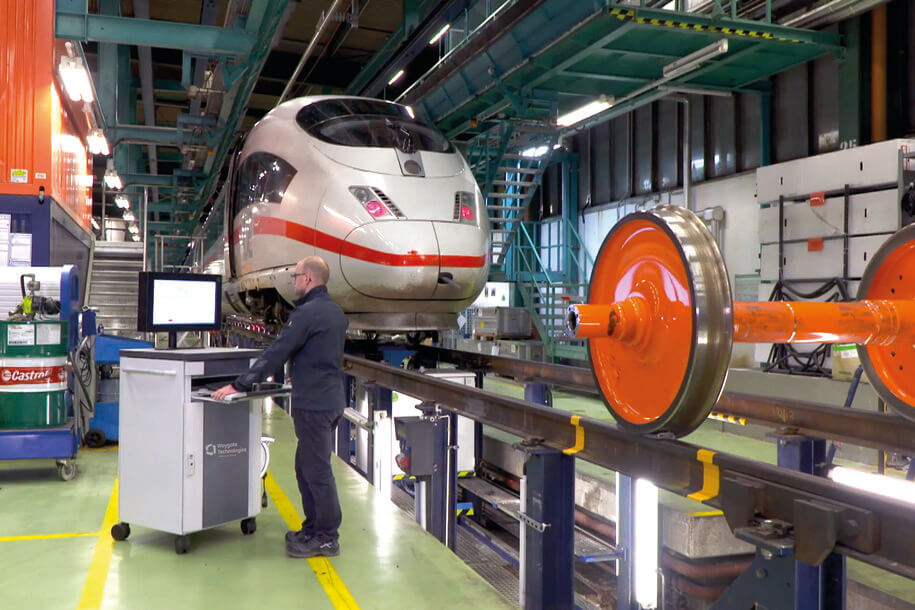
超声检测赋能铁路安全
铁路车轮在高速和重载的巨大压力下,必须进行严格的检查以确保安全。超声波检测是全球铁路标准所要求的,能够有效检测这些复杂几何形状中的潜在缺陷。先进的检测系统现在已支持轮对在线检测,即无需拆卸即可进行全面扫描。矩阵技术凭借其动态调整波束参数的能力,使检测更加快速和准确,从而减少故障风险,提高铁路系统的整体安全性。
自动化控制与报告系统的集成进一步优化了检测流程。例如,单组轮对检测周期仅需20分钟,其中有效检测时间90秒,在保障效率的同时最大限度减少误差。针对轮对关键区域的复合投影检测,可有效消除几何回波干扰,结合自动缺陷识别(ADR)技术,大幅提升了缺陷判定精度与操作便捷性。
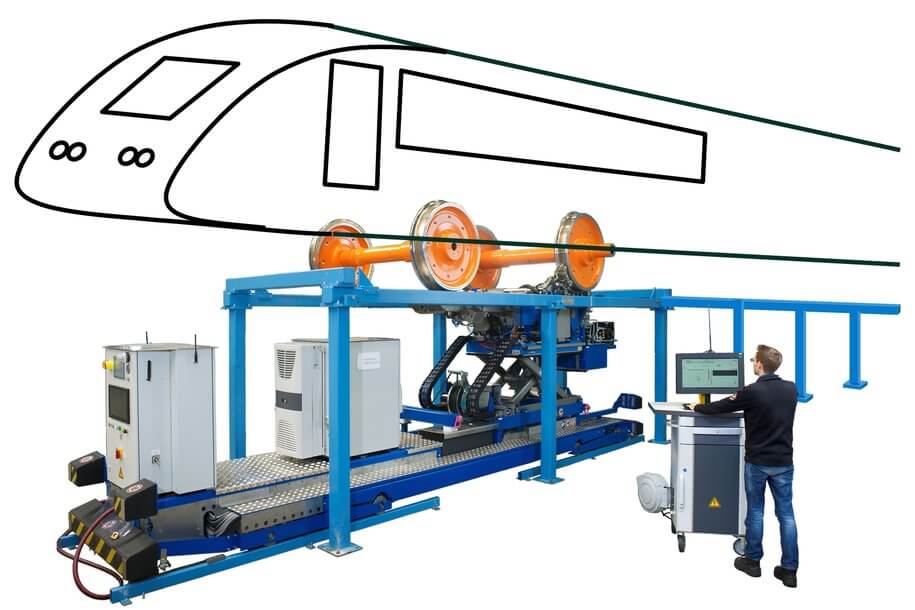
便携式技术赋能现场检测
在需要人工手动检测的行业中,如航空航天,便携式相控阵与矩阵超声技术的突破具有里程碑意义。此类设备将相控阵处理能力集成于探头内部,无需额外设备即可实现轻量化、多功能、低成本的检测。配合先进滚轮探头,特别适用于航空航天、空间探索及风能领域的大型非平面复合材料检测。
现代技术将相控阵电子模块缩至拇指一半大小的芯片,支持通过平板或电脑的USB接口供电。这一创新不仅提升技术效率,更降低了使用成本,为一线检测人员提供了前所未有的灵活性与便利性。
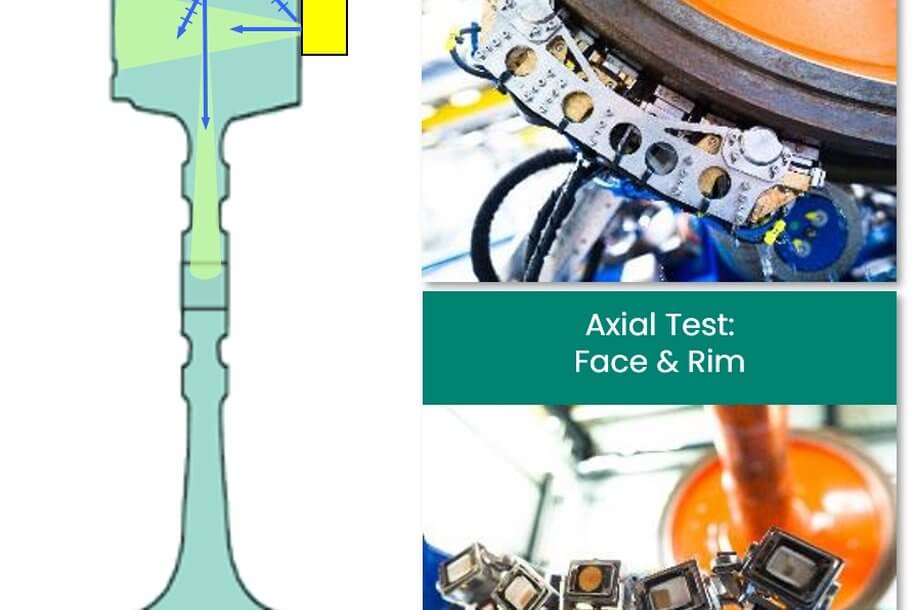
超声检测的未来展望
智能技术的崛起标志着工业超声检测的重大飞跃。起源于医疗行业的创新正在通过提升检测质量、减少人为误差、优化整体效率,重塑工业应用。
面对行业日益严格的监管要求、专业技术人员的短缺以及深度检测需求的增长,智能检测技术的普及势不可挡。矩阵技术与电子元件微型化作为技术革命的前沿,正引领超声检测未来的发展方向。
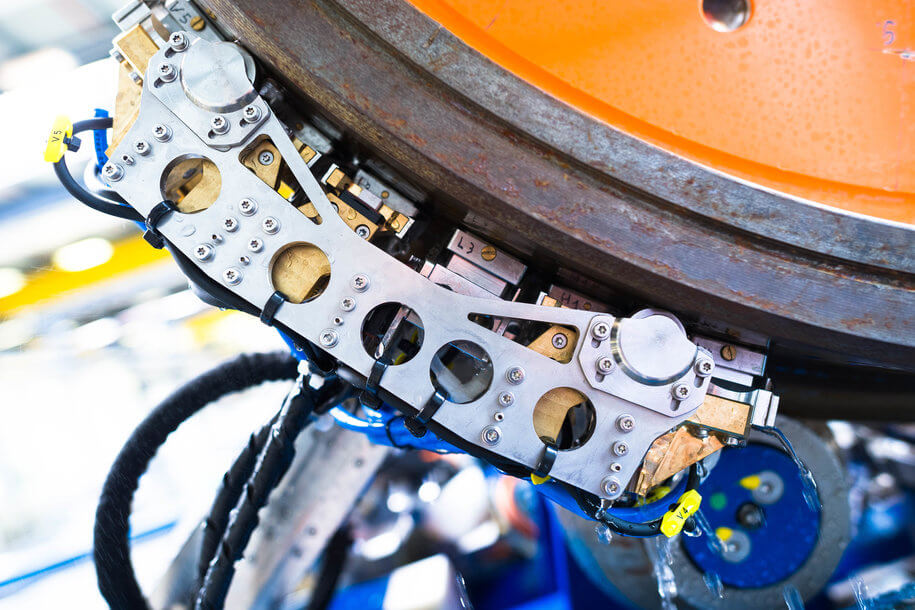
新闻中心:
- 无损检测的最新进展:提升检测效率
- 对话与创新 | 微纳米成像研讨会回顾
- 追求精准 | 方程式赛车单体壳应用
- 从布尔诺到太空 | 为TROLL卫星关键部件质量保驾护航
- 利用检测数据加速产品演进
- 工业计算机断层扫描与计量学的进展
- 计算机断层扫描图像 vs 传统X光片
- 虚拟考古学的新视角
- 新型柔性数字X射线探测器上市:DXR Flex
- 如何描述CT图像中的图像质量?
- 维睿泰与GE航空航天公司联合提供全新的检测解决方案
- 维睿泰荣膺Kaizen运营卓越奖
- 工业CT扫描容积提升方案|大尺寸物体检测技术突破
- CT中需要多少投影?
- 建筑结构无损检测利器:数字射线成像技术 – 维睿泰
- 启停电池100%质检方案-V|tome|x M Neo应用
- 灵活探头 | 轻松应对复杂检测环境
- 多面应用:从航空发动机到汽车制造
- AI智能加持的工业内窥镜 | Mentor Visual iQ+重磅登场
- Phoenix Nanotom M
- 用户案例 | 焊嘴镀层厚度精准测量
- 技术科普 | 可变FDD的三大核心优势
- 用户案例 | 解决大尺寸PCB检测难题
- 工业CT检测新突破:Datos|x 3.1 提升成像质量与效率
- 维睿泰携手美国能源部 助推电动车电池循环经济
- 内窥镜租赁服务:高效、灵活的无损检测解决方案
- 超声波检测技术助力低空经济
- Flash!图像增强技术对数字射线原始图像和测量准确性的影响
- 数字化射线检测技术助力文保研究
- 航空航天“守护者”:工业CT技术赋能航空检测
- 研讨会回顾:Phoenix助力汽车安全与智能检测
- Mesofocus CT在iWP初登场
- Phoenix 25+周年庆典圆满落幕
- 维睿泰三款顶尖CR扫描仪
- 数字射线CR/DR技术,电力GIS检测的利器!
- 探索X射线和CT技术如何提升电池回收与再利用
- Phoenix系列最新X射线和CT检测系统产品家族
- 徐华东会见美国贝克休斯公司客人
- Ben Linke中国行:半导体与航空航天检测技术发展洞察
- Krautkrämer自动化超声波检测系统
- UTTM服务团队两返现场,快速修复某司宕机设备
- USM100 & InspectionWorks助力企业实现更高效的太空探索
- 韩国华城电池厂悲惨火灾
- 我们认真做科普:什么是X射线?
- DXR S140: 全新的数字平板探测器
- 先进封装X-ray检测解决方案:Neo系列助力高良率
- 工业射线照相技术全解析:CR与DR成像原理及应用
- Krautkrämer RotoArray comPAct便携超声检测解决方案
- 龙腾龙年 追梦未来: PPS中国2024年会简报
- Ben Linke
- 李冉专访:慧质兰心 才情横溢
- 我们认真做科普:不同壁厚射线透照调整方法
- InspectionWorks引领工业检测进入新时代
- 超声波反射器效果评估与DGS图表应用指南
- 探究声波与界面相互作用的过程与结果
- 超声波检测过程中,声束特征的重要作用
- 超声波测量技术中分贝的作用是什么?
- 声场在超声波脉冲技术中的作用与影响
- 超声波探头分为哪些不同类型?
- 超声波检测材料原理与应用技术全解析
- 超声波检测的组成部分及其工作原理
- 有哪些基本方法用于超声波检测?
- 超声波检测应用领域全解析:交通、医疗、制造业
- Waygate Technologies全球射线检测服务
- 超声波检测的组件和基本原理
- 超声波的检测方法有哪些?
- Krautkramer RotoArray comPAct超声波相控阵探头便携高效
- 维睿泰与赛默飞合作:电池与材料无损检测新突破
- 超声波检测的应用范围是什么
- 工业射线系统中国区售后服务团队
- 维睿泰:风电USM100超声波检测+汽车胶接点焊无损检测解决方案
- 工业内窥镜厂家:如何选购适合您的工业内窥镜?
- 工业内窥镜厂家:如何选购适合您的工业内窥镜?
- 工业CT无损检测:改变工业质量控制的颠覆性技术
- 超声波探头型号和参数:选择正确的设备以提升您的检测效率
- Seifert固定式X射线机全新亮相
- 什么是管道机器人:关键功能和优点解析
- phoenix vtomex s240 多功能工业 2D X射线成像和3D CT系统
- 模块化水浸检测系统 KT-1000
- 无损探伤检测工业CT及X射线系统解决方案
- 锂电池行业无损检测解决方案
- Krautkrämer SpotVision
- Mentor Visual iQ 高清工业内窥镜
- Everest Mentor Flex 高清工业内窥镜
- Krautkramer USM100探伤仪
- 无损检测公司 Waygate Technologies
- 工业内窥镜检测技术优缺点对比
- 工业内窥镜的定义以及内窥镜的正确使用方法
- 贝克休斯公司简介:为推进能源发展的高效运转,推进能源清洁化进程。
- 贝克休斯检测科技公司介绍
- 内窥检测与AI技术结合,提升智能工业内窥镜工作效率!