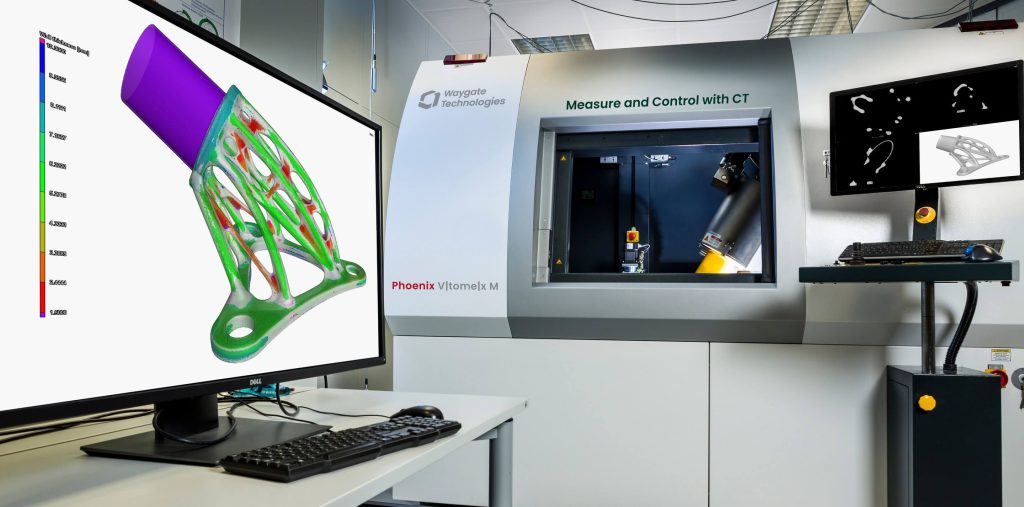
增材制造应用中的计算机断层扫描
工业CT技术简介:增材制造的3D检测与计量
计算机断层扫描(Computed Tomography, CT)为增材制造(Additive Manufacturing, AM)中复杂零件的检测与测量提供了核心工具。通过将最终产品与原始三维设计进行对比,CT技术能够确保所有关键内部尺寸均被精准复现。在性能与安全要求不可妥协的行业中,该技术尤为重要。
增材制造的意义
增材制造标志着工程领域的一次变革性转变,其重要性堪比铸造工艺与机床的诞生。它彻底革新了零件设计、快速样品制作及复杂部件的生产方式。这些发展在过去是无法通过单一零件实现的,现在需要精确的质量控制。在这里,工业计算机断层扫描(CT)技术的三维检测和计量变得不可或缺。
工业计算机断层扫描技术解析
工业CT通过采集大量二维X射线图像,经重建生成三维体积数据。待检物体被置于精密转台上,在密闭舱内接受高能辐射照射。物体旋转过程中,辐射被吸收并形成二维投影,由探测器捕获后,通过数学算法重建为精细的三维模型。
扇形束与锥束CT技术对比
工业CT主要采用扇形束与锥束两种技术,二者原理相同,但辐射方向与数据采集方式存在差异:
工业CT主要采用两种技术:风束CT和锥束CT。两者基于相同的基本原理,但在辐射方向和数据检测方法上有所不同。
风束CT通过旋转和线性移动X射线束,将工件切割成薄片。一个准直的线型探测器捕捉这些切片,然后将其重建为三维体积。虽然这种方法对高密度金属零件有效,但由于散射辐射伪影,它的速度较慢。
相比之下,锥束CT使用一个平面探测器,在一次旋转中捕获整个工件。虽然这种技术更快,但它对散射辐射的敏感性更高,因此生成的图像精度较风束CT差。
增材制造计量的挑战
增材制造通过分层堆积材料创建三维部件,与减材制造不同,各种增材制造技术包括烧结、激光或电子束熔化金属粉末,以及立体光刻。
计算机断层扫描(CT)可以应用于这些技术的各个阶段,从原材料质量控制到最终部件计量。例如,高分辨率纳米聚焦CT能够通过分析颗粒大小、形状和孔隙度来确保粉末的一致性,这些检测数据会影响最终成品的密度以及发现可能存在的缺陷。
确保工艺精度
CT扫描在检测增材制造(AM)的缺陷检测过程中也至关重要。粉末质量或层叠过程中的瑕疵可能会导致空洞或杂质。这些缺陷在初始阶段可能符合公差,但在热处理后可能会引起显著的变形。CT技术可以识别这些缺陷的大小、位置和分布,从而帮助优化工艺。
最终零件检测的精度
对成品进行CT检测可以验证制造的产品是否与初始的3D设计相符。这包括对内部特征、壁厚以及其他使用传统方法难以测量的方面进行尺寸分析。先进的CT扫描仪可以实现几微米以内的测量精度,从而确保精准的质量控制。
增材制造CT技术的增强方向
制造业持续追求提速不减质的生产模式,CT技术的提升使其成为可能,支持设计优化、产能提升与组件验证。
CT硬件与软件的创新
近年来,CT系统取得了显著的进步,包括高分辨率纳米聚焦扫描和散射修正技术。例如,散射修正技术能够减少锥形束CT中由散射辐射引起的伪影,从而提升图像质量,达到与扇形束CT相媲美的效果,同时显著缩短扫描时间。
此外,新的探测器提供了高分辨率的图像,能够检测到微小的缺陷。先进的软件现在将系统控制、数据采集、体积重建和准确的表面数据生成等所有必要功能整合在一起。更高的X射线功率集中在更小的区域上,使得分辨率得以提升或扫描速度加快。
增材制造与CT技术的未来
尽管增材制造仍在不断发展,但它已经从快速样品制造转向生产,特别是在航空航天领域。它在创造具有无与伦比的内部复杂性的部件方面的潜力,现已在各行各业得到了实现。随着增材制造技术的进步,CT技术也在不断发展,目前CT技术已推出产线用在线设备,实现生产现场的自动化全检。
结论
随着增材制造技术在航空航天、汽车等工业领域扩展,工业CT的作用将愈发关键。CT技术将继续应对不断变化的检验和质量控制挑战,确保未来产品的完整性和性能。
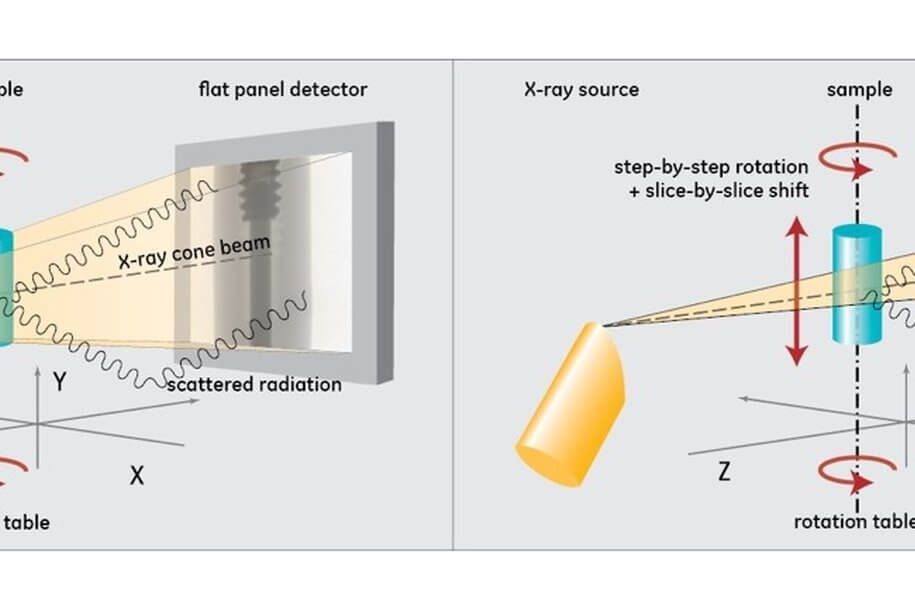
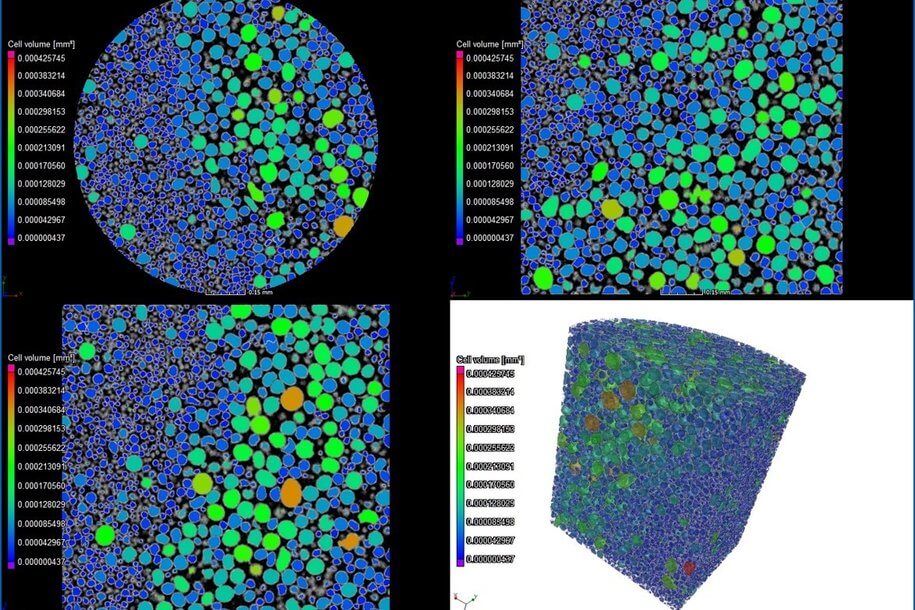
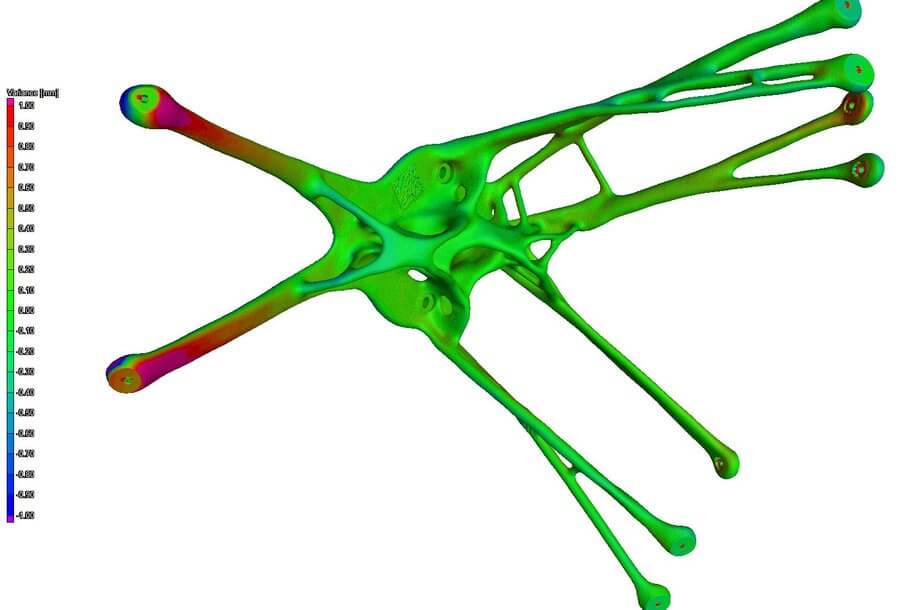
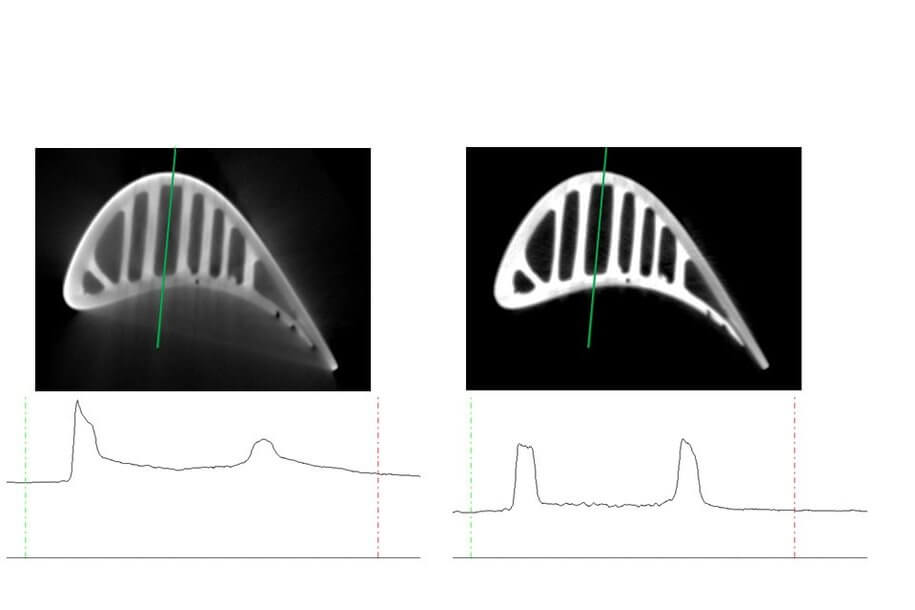
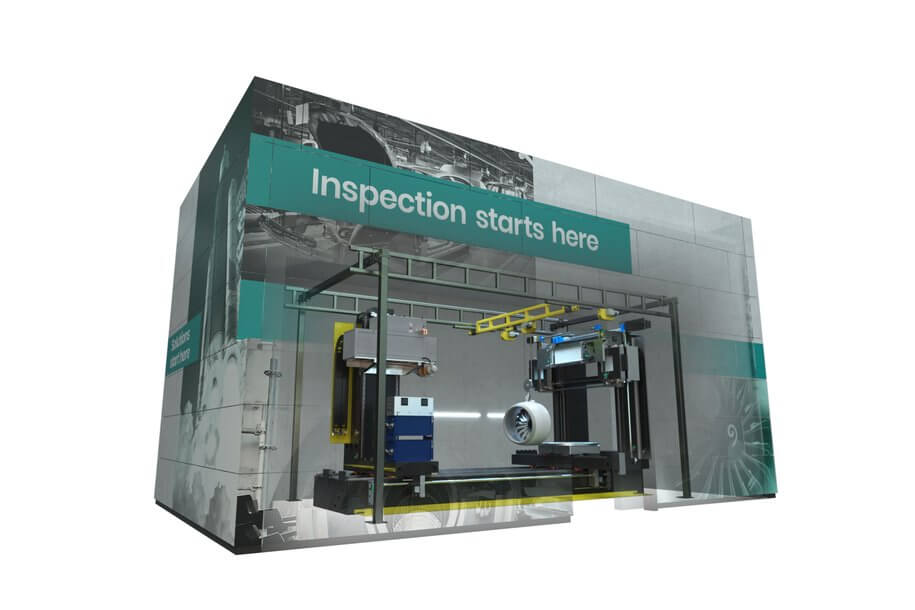
新闻中心:
- 无损检测:推动汽车行业质量升级
- 数字化转型之路:利用数据赋能工业检测
- 无损检测中的远程协作:技术创新
- 从数字孪生到数字三胞胎:推动无损检测与检测技术的革新
- 能源转型与工业检测的必要性
- 使用CT的无损检测:电子检测技术的进步
- 智能检验:工业超声检测的进展
- 无损检测的最新进展:提升检测效率
- 对话与创新 | 微纳米成像研讨会回顾
- 追求精准 | 方程式赛车单体壳应用
- 从布尔诺到太空 | 为TROLL卫星关键部件质量保驾护航
- 利用检测数据加速产品演进
- 工业计算机断层扫描与计量学的进展
- 计算机断层扫描图像 vs 传统X光片
- 虚拟考古学的新视角
- 新型柔性数字X射线探测器上市:DXR Flex
- 如何描述CT图像中的图像质量?
- 维睿泰与GE航空航天公司联合提供全新的检测解决方案
- 维睿泰荣膺Kaizen运营卓越奖
- 工业CT扫描容积提升方案|大尺寸物体检测技术突破
- CT中需要多少投影?
- 建筑结构无损检测利器:数字射线成像技术 – 维睿泰
- 启停电池100%质检方案-V|tome|x M Neo应用
- 灵活探头 | 轻松应对复杂检测环境
- 多面应用:从航空发动机到汽车制造
- AI智能加持的工业内窥镜 | Mentor Visual iQ+重磅登场
- Phoenix Nanotom M
- 用户案例 | 焊嘴镀层厚度精准测量
- 技术科普 | 可变FDD的三大核心优势
- 用户案例 | 解决大尺寸PCB检测难题
- 工业CT检测新突破:Datos|x 3.1 提升成像质量与效率
- 维睿泰携手美国能源部 助推电动车电池循环经济
- 内窥镜租赁服务:高效、灵活的无损检测解决方案
- 超声波检测技术助力低空经济
- Flash!图像增强技术对数字射线原始图像和测量准确性的影响
- 数字化射线检测技术助力文保研究
- 航空航天“守护者”:工业CT技术赋能航空检测
- 研讨会回顾:Phoenix助力汽车安全与智能检测
- Mesofocus CT在iWP初登场
- Phoenix 25+周年庆典圆满落幕
- 维睿泰三款顶尖CR扫描仪
- 数字射线CR/DR技术,电力GIS检测的利器!
- 探索X射线和CT技术如何提升电池回收与再利用
- Phoenix系列最新X射线和CT检测系统产品家族
- 徐华东会见美国贝克休斯公司客人
- Ben Linke中国行:半导体与航空航天检测技术发展洞察
- Krautkrämer自动化超声波检测系统
- UTTM服务团队两返现场,快速修复某司宕机设备
- USM100 & InspectionWorks助力企业实现更高效的太空探索
- 韩国华城电池厂悲惨火灾
- 我们认真做科普:什么是X射线?
- DXR S140: 全新的数字平板探测器
- 先进封装X-ray检测解决方案:Neo系列助力高良率
- 工业射线照相技术全解析:CR与DR成像原理及应用
- Krautkrämer RotoArray comPAct便携超声检测解决方案
- 龙腾龙年 追梦未来: PPS中国2024年会简报
- Ben Linke
- 李冉专访:慧质兰心 才情横溢
- 我们认真做科普:不同壁厚射线透照调整方法
- InspectionWorks引领工业检测进入新时代
- 超声波反射器效果评估与DGS图表应用指南
- 探究声波与界面相互作用的过程与结果
- 超声波检测过程中,声束特征的重要作用
- 超声波测量技术中分贝的作用是什么?
- 声场在超声波脉冲技术中的作用与影响
- 超声波探头分为哪些不同类型?
- 超声波检测材料原理与应用技术全解析
- 超声波检测的组成部分及其工作原理
- 有哪些基本方法用于超声波检测?
- 超声波检测应用领域全解析:交通、医疗、制造业
- Waygate Technologies全球射线检测服务
- 超声波检测的组件和基本原理
- 超声波的检测方法有哪些?
- Krautkramer RotoArray comPAct超声波相控阵探头便携高效
- 维睿泰与赛默飞合作:电池与材料无损检测新突破
- 超声波检测的应用范围是什么
- 工业射线系统中国区售后服务团队
- 维睿泰:风电USM100超声波检测+汽车胶接点焊无损检测解决方案
- 工业内窥镜厂家:如何选购适合您的工业内窥镜?
- 工业内窥镜厂家:如何选购适合您的工业内窥镜?
- 工业CT无损检测:改变工业质量控制的颠覆性技术
- 超声波探头型号和参数:选择正确的设备以提升您的检测效率
- Seifert固定式X射线机全新亮相
- 什么是管道机器人:关键功能和优点解析
- phoenix vtomex s240 多功能工业 2D X射线成像和3D CT系统
- 模块化水浸检测系统 KT-1000
- 无损探伤检测工业CT及X射线系统解决方案
- 锂电池行业无损检测解决方案
- Krautkrämer SpotVision
- Mentor Visual iQ 高清工业内窥镜
- Everest Mentor Flex 高清工业内窥镜
- Krautkramer USM100探伤仪
- 无损检测公司 Waygate Technologies
- 工业内窥镜检测技术优缺点对比
- 工业内窥镜的定义以及内窥镜的正确使用方法
- 贝克休斯公司简介:为推进能源发展的高效运转,推进能源清洁化进程。
- 贝克休斯检测科技公司介绍
- 内窥检测与AI技术结合,提升智能工业内窥镜工作效率!