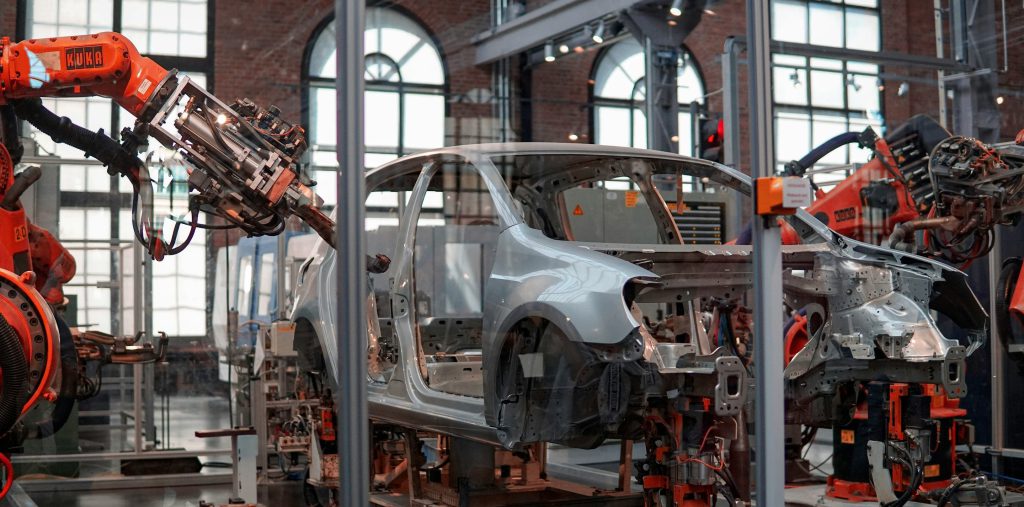
无损检测:推动汽车行业质量升级
引言
汽车行业作为全球具活力的行业之一,每年生产超过7000万辆汽车,且技术复杂性不断攀升。该行业通过贡献约3.4万亿美元的年产值推动经济增长,还为其他领域设定了技术标准。然而,尽管生产效率和质量往往存在相互冲突的需求,无损检测(NDT)在平衡这两者方面的作用仍然被大多数人忽视。
汽车行业变革趋势
当前汽车行业正经历深刻变革。全球出行的趋势,加上严格的排放和燃油消耗法规,迫使制造商大力投资于新型驱动系统,如全电动或氢动力汽车,以及优化传统发动机。此外,消费者对提升驾驶舒适性的需求,包括连接性和自动驾驶,进一步推动创新。制造商还必须通过数字化优化车辆生产过程,并提升产品质量,以应对这些挑战。这些相互交织的压力将在未来几年内彻底改变汽车行业。
汽车生产的可持续性要求
除上述直接挑战外,全球变暖等更广泛的环境问题将影响汽车生产未来。可持续性必须融入个人行为工业生产实践,资源的高效管理和废物减少将成为产品生命周期中的关键组成部分,进一步影响汽车制造业的发展。
汽车行业质量控制的演进
在汽车行业的早期,质量控制相对简单。大规模生产依赖于工艺的可重复性来确保一致性,而一致性又与质量挂钩。为了确保生产标准,随机抽查通常会涉及到对组件的破坏性检查。例如,X射线检查长期以来被用于检查铸件和发动机缸体。
尽管技术进步,破坏性检测仍因速度快和固有生产习惯的延续,但会造成大量废料与高昂返修成本。
无损检测的崛起
幸运的是,无损检测技术的进步促使如今已经可以快速、可靠的检测方法,同时减少材料浪费并提升可持续性。许多无损检测方法是数字化的,便于与现有生产流程无缝集成。
视觉检测仍然是无损检测的基础,通常在直接接触部件受限时,使用视频探头进行辅助,其广泛应用于终检、引擎开发与密封性测试。
射线检测,使用X射线技术和数字探测器,仍用于发动机缸体与轮毂等安全关键部件的检测。从传统的二维射线摄影转向数字射线计算机断层扫描(CT)显著提高了检测质量。CT技术最初源自医学影像,经过二十年的发展,已成为汽车制造中的重要技术,逐渐从实验室环境转移到生产线中。自动缺陷识别(ADR)和人工智能(AI)等创新进一步自动化了这些过程,尤其是在电池单体检测等应用中。
扩展的NDT技术
涡流检测是汽车行业另一广泛应用技术,用于检测主缸、轴承座圈与活塞等部件的裂纹与硬度。现代涡流系统在高频下运行,支持高速产线快速检测,并实现自动化的合格/不合格控制。
同样地,超声检测在完整性测试,尤其是焊缝检测中应用渐增,正逐步替代破坏性抽检。
无损检测在汽车制造中的未来
成本压力与新材料的引入加速NDT技术推广。新材料常需激光焊接、粘接等新连接技术,亟待创新的检测解决方案。这些方案需无缝融入产线,提升效率并降低报废与返修成本,从而增强可持续性。
如今,许多工作都可以利用自动化检测,这不仅能够提高效率,还能利用检测数据改进过程控制。现代的无损检测方法提供了清晰易懂的显示和报告,生成大量数据。先进的数据管理、分析和存储软件解决方案,以及远程监控和诊断功能,对于处理这些信息至关重要,甚至可以进行不同检测方法之间的对比分析。
结论
以上技术突破与理念的转变为汽车制造商与供应商带来福音。无损检测解决方案通过减少报废与返修降低成本,凭借精准可靠数据缩短样品开发周期
新闻中心:
- 数字化转型之路:利用数据赋能工业检测
- 增材制造应用中的计算机断层扫描
- 无损检测中的远程协作:技术创新
- 从数字孪生到数字三胞胎:推动无损检测与检测技术的革新
- 能源转型与工业检测的必要性
- 使用CT的无损检测:电子检测技术的进步
- 智能检验:工业超声检测的进展
- 无损检测的最新进展:提升检测效率
- 对话与创新 | 微纳米成像研讨会回顾
- 追求精准 | 方程式赛车单体壳应用
- 从布尔诺到太空 | 为TROLL卫星关键部件质量保驾护航
- 利用检测数据加速产品演进
- 工业计算机断层扫描与计量学的进展
- 计算机断层扫描图像 vs 传统X光片
- 虚拟考古学的新视角
- 新型柔性数字X射线探测器上市:DXR Flex
- 如何描述CT图像中的图像质量?
- 维睿泰与GE航空航天公司联合提供全新的检测解决方案
- 维睿泰荣膺Kaizen运营卓越奖
- 工业CT扫描容积提升方案|大尺寸物体检测技术突破
- CT中需要多少投影?
- 建筑结构无损检测利器:数字射线成像技术 – 维睿泰
- 启停电池100%质检方案-V|tome|x M Neo应用
- 灵活探头 | 轻松应对复杂检测环境
- 多面应用:从航空发动机到汽车制造
- AI智能加持的工业内窥镜 | Mentor Visual iQ+重磅登场
- Phoenix Nanotom M
- 用户案例 | 焊嘴镀层厚度精准测量
- 技术科普 | 可变FDD的三大核心优势
- 用户案例 | 解决大尺寸PCB检测难题
- 工业CT检测新突破:Datos|x 3.1 提升成像质量与效率
- 维睿泰携手美国能源部 助推电动车电池循环经济
- 内窥镜租赁服务:高效、灵活的无损检测解决方案
- 超声波检测技术助力低空经济
- Flash!图像增强技术对数字射线原始图像和测量准确性的影响
- 数字化射线检测技术助力文保研究
- 航空航天“守护者”:工业CT技术赋能航空检测
- 研讨会回顾:Phoenix助力汽车安全与智能检测
- Mesofocus CT在iWP初登场
- Phoenix 25+周年庆典圆满落幕
- 维睿泰三款顶尖CR扫描仪
- 数字射线CR/DR技术,电力GIS检测的利器!
- 探索X射线和CT技术如何提升电池回收与再利用
- Phoenix系列最新X射线和CT检测系统产品家族
- 徐华东会见美国贝克休斯公司客人
- Ben Linke中国行:半导体与航空航天检测技术发展洞察
- Krautkrämer自动化超声波检测系统
- UTTM服务团队两返现场,快速修复某司宕机设备
- USM100 & InspectionWorks助力企业实现更高效的太空探索
- 韩国华城电池厂悲惨火灾
- 我们认真做科普:什么是X射线?
- DXR S140: 全新的数字平板探测器
- 先进封装X-ray检测解决方案:Neo系列助力高良率
- 工业射线照相技术全解析:CR与DR成像原理及应用
- Krautkrämer RotoArray comPAct便携超声检测解决方案
- 龙腾龙年 追梦未来: PPS中国2024年会简报
- Ben Linke
- 李冉专访:慧质兰心 才情横溢
- 我们认真做科普:不同壁厚射线透照调整方法
- InspectionWorks引领工业检测进入新时代
- 超声波反射器效果评估与DGS图表应用指南
- 探究声波与界面相互作用的过程与结果
- 超声波检测过程中,声束特征的重要作用
- 超声波测量技术中分贝的作用是什么?
- 声场在超声波脉冲技术中的作用与影响
- 超声波探头分为哪些不同类型?
- 超声波检测材料原理与应用技术全解析
- 超声波检测的组成部分及其工作原理
- 有哪些基本方法用于超声波检测?
- 超声波检测应用领域全解析:交通、医疗、制造业
- Waygate Technologies全球射线检测服务
- 超声波检测的组件和基本原理
- 超声波的检测方法有哪些?
- Krautkramer RotoArray comPAct超声波相控阵探头便携高效
- 维睿泰与赛默飞合作:电池与材料无损检测新突破
- 超声波检测的应用范围是什么
- 工业射线系统中国区售后服务团队
- 维睿泰:风电USM100超声波检测+汽车胶接点焊无损检测解决方案
- 工业内窥镜厂家:如何选购适合您的工业内窥镜?
- 工业内窥镜厂家:如何选购适合您的工业内窥镜?
- 工业CT无损检测:改变工业质量控制的颠覆性技术
- 超声波探头型号和参数:选择正确的设备以提升您的检测效率
- Seifert固定式X射线机全新亮相
- 什么是管道机器人:关键功能和优点解析
- phoenix vtomex s240 多功能工业 2D X射线成像和3D CT系统
- 模块化水浸检测系统 KT-1000
- 无损探伤检测工业CT及X射线系统解决方案
- 锂电池行业无损检测解决方案
- Krautkrämer SpotVision
- Mentor Visual iQ 高清工业内窥镜
- Everest Mentor Flex 高清工业内窥镜
- Krautkramer USM100探伤仪
- 无损检测公司 Waygate Technologies
- 工业内窥镜检测技术优缺点对比
- 工业内窥镜的定义以及内窥镜的正确使用方法
- 贝克休斯公司简介:为推进能源发展的高效运转,推进能源清洁化进程。
- 贝克休斯检测科技公司介绍
- 内窥检测与AI技术结合,提升智能工业内窥镜工作效率!